Introduction
The earliest research on laser cleaning technology can be traced back to the 1960s. In 1965, the Nobel laureate Schawlow irradiated a piece of paper printed with ink using a pulsed laser. The ink characters on the paper surface vaporized rapidly, while the paper itself remained undamaged. He proposed the term “laser eraser” for the first time, as shown in the figure. In 1969, Bedair and others used a Q-switched laser to remove oxygen and sulfur contamination on the surface of nickel and put forward the concept of laser cleaning. In 1973, the Asmus team was the first to report laser cleaning of cultural relics. They carried out laser cleaning on a variety of cultural relics, including the statue of Leonardo da Vinci and murals. In 1974, Fox used a Q-switched neodymium-glass laser to effectively remove the paint layer on the resin and metal substrates. In the 1980s, for the new technology of electron-beam projection lithography, when preparing the mask plate, the surface of the mask plate would inevitably be contaminated with particulate pollutants, resulting in defective products. However, traditional cleaning technologies such as ultrasonic cleaning, mechanical cleaning, and chemical cleaning could not remove the particulate pollutants. In 1982, Zapka and others irradiated the mask plate with a focused laser and successfully cleaned off the attached pollutants without causing the slightest damage to the mask pattern. It can be seen that the invention of laser cleaning technology was mainly aimed at cleaning the tiny particles on the surface of semiconductors. Its development and the progress of semiconductor technology have promoted each other. At the same time, this technology is also constantly exploring applications in other fields.
In modern industry, cleaning technology has always been an indispensable part of the production process. Traditional cleaning methods, such as chemical cleaning, mechanical grinding, and sandblasting, can meet cleaning needs to a certain extent, but they also bring issues such as environmental pollution, resource waste, and health risks. With the advancement of technology, laser cleaning technology has emerged as an efficient, environmentally friendly, and precise cleaning solution. This article will delve into the principles, application areas, advantages, and future development trends of laser cleaning, providing a comprehensive understanding of this green cleaning revolution in modern industry.
Categories of Laser Cleaning
According to different mechanisms of action, direct contact can be divided into three types:
(1) The pulsed laser directly irradiates the surface of the object, and the high-energy characteristics of the laser are used to achieve decontamination. Both the substrate and the contaminants increase in temperature due to the absorption of laser energy. The absorption rate of the surface contaminants to the laser is significantly higher than that of the substrate to the laser. In the central area where the laser acts, the contaminants are removed due to vaporization, ablation, photochemical reactions, thermal decomposition, etc. In the marginal area where the laser acts, the contaminants are removed due to thermal stress, thermal shock, and physical fracture.
(2) A liquid film is pre-coated on the surface of the object to be cleaned. The laser directly irradiates the liquid film, which absorbs the laser energy and heats up rapidly, generating a strong impact force to remove the contaminants on the surface of the substrate.
(3) A short-pulse laser irradiates the surface of the substrate. Due to the different thermal expansion coefficients of different materials, under the irradiation of the short-pulse laser, the surface contaminants and the substrate will undergo thermal expansion and contraction of different degrees at a high frequency, generating an oscillating effect, causing the contaminants to fall off from the surface of the substrate.
The laser cleaning method of indirect contact does not directly contact the surface to be cleaned. The laser is emitted in a direction parallel to the surface. After being focused by a lens, the high energy causes the gas to be broken down, forming a laser plasma. During the rapid expansion of the plasma, it comes into contact with the contaminants, and the generated impact force causes the contaminants to separate from the surface. The cleaning objects of this method are submicron or nanoscale particles, and the process requirements are very strict. It is necessary to ensure that the air can be ionized, and at the same time, a suitable distance should be maintained between the laser and the surface of the substrate to ensure that the impact force acting on the particles is large enough.
Principles of Laser Cleaning Machine
Laser cleaning is a technology that uses high-energy laser beams to irradiate the surface of an object, removing surface contaminants through photothermal or photochemical effects. Its core principle lies in the high energy density and short pulse characteristics of the laser beam, which can heat contaminants to evaporation or peeling in an extremely short time without damaging the substrate. One of the key terms in laser cleaning is “high energy density,” which enables the laser to precisely control the cleaning process at a microscopic level, ensuring cleaning effectiveness while protecting the integrity of the substrate.
The purpose of laser cleaning is to remove the surface material without damaging the underlying material. Although a laser can cut through a steel plate several inches thick, cleaning work requires a lighter touch and an understanding of the ablation threshold. Each material has an ablation threshold, which effectively defines the amount of energy required to vaporize the material. By keeping the energy below the threshold, the bulk material will not be damaged. However, even a single exceedance of the threshold will affect the bulk material. Fortunately, compared with metals such as steel and aluminum, the materials that most manufacturers need to remove (such as rust, oil, and coatings) have a lower ablation threshold. Nevertheless, to avoid damaging the substrate, careful adjustment of the laser parameters, such as wavelength and pulse energy, is still required. Precise control of the spot size and shape also helps to minimize overlap when the beam is scanned, thereby improving the efficiency of laser cleaning.
The laser cleaning process can be divided into the following steps: first, the laser beam is focused onto the surface to be cleaned through an optical system, forming a high-energy-density spot; second, the laser energy is absorbed by the surface contaminants, causing them to rapidly heat up and evaporate or peel off; finally, the evaporated or peeled-off contaminants are removed by airflow or a vacuum system, completing the cleaning process. This process is not only efficient but also environmentally friendly, as laser cleaning does not require chemical solvents or produce harmful waste.
Application Areas of Laser Cleaning Machine
Laser cleaning technology has a wide range of applications, especially the high-power machine like 3000W laser cleaning machine, covering industries such as aerospace, automotive manufacturing, electronics, and cultural heritage preservation. In the aerospace sector, laser cleaning is used to remove oxidation layers and coatings from aircraft engine blades, ensuring efficient engine operation. In automotive manufacturing, laser cleaning can eliminate oxidation and oil stains at welding points on car bodies, improving welding quality and appearance. In the electronics industry, laser cleaning is used to remove tiny contaminants from circuit boards, ensuring the reliability and performance of electronic components.
Another key term in laser cleaning is “precision cleaning.” Laser cleaning technology can achieve cleaning precision at the micron level, making it particularly suitable for cleaning complex shapes and small components. For example, in cultural heritage preservation, laser cleaning is used to remove dirt and rust from the surfaces of ancient artifacts, restoring their original appearance. This precision cleaning not only protects the historical value of the artifacts but also avoids potential damage caused by traditional cleaning methods.
At present, laser cleaning technology has been applied in many manufacturing fields such as microelectronics, rail transit, aviation, shipping, and automobiles. Its typical applications mainly include the removal of particulate pollutants, rust, paint, oil stains, and oxide films, etc., and it shows a diversified development trend. It has also been effectively tried and successfully applied in the field of cultural relic cleaning and protection.
(1) Laser rust removal: Metal objects are prone to forming a rust layer when exposed to a humid air environment for a long time. The existence of the rust layer not only affects the performance in use and accelerates corrosion, but also has a serious impact on the safety and service life of the objects. Traditional rust removal methods include shot blasting and chemical cleaning. These two methods are relatively efficient and have mature technologies. However, they will cause pollution to the environment and are harmful to the health of operators. Therefore, the laser cleaning method has received widespread attention. It is green and environmentally friendly, highly efficient, high-precision, and low-cost, and can replace conventional cleaning methods. It has gradually been applied in the industrial field.
(2)Laser paint stripping: Large-scale equipment such as ships, aircraft, and bridges require regular repainting. Before repainting, the aged and damaged paint needs to be removed first, and this process is called paint removal. During the paint removal process, it is necessary to thoroughly remove the aged paint without damaging the substrate. However, traditional paint removal methods generally have disadvantages such as low efficiency, high energy consumption, insufficient precision in the removal thickness of the paint layer, and poor surface uniformity, and they cannot meet the requirements for the controllable removal of the paint layer. Compared with traditional paint removal technologies, the laser cleaning technology is green, safe, and environmentally friendly, causes little damage to the substrate, has high efficiency, and the laser positioning is accurate. It is suitable for structural parts with complex shapes such as those of aircraft and ships.
(3)Laser cleaning of electronic components: Tiny contaminants on electronic components can reduce electronic efficiency and cause damage to electronic circuit boards. With the development of science and technology, semiconductors and microelectronic devices are becoming smaller and smaller, and the particles that need to be cleaned are also getting tinier, increasing the difficulty of cleaning. Traditional water washing and ultrasonic cleaning methods cannot achieve such a high-precision cleaning effect. Therefore, laser cleaning brings new hope and has become the best cleaning method.There are many applications of lasers in the cleaning of electronic components, such as electronic circuit boards, silicon wafers, integrated circuits, flexible circuits, optoelectronic devices, etc. With the development of technology, these devices have increased in integration, with more and more pins and smaller and smaller holes. Traditional cleaning methods are difficult to be effective. Laser cleaning, due to its advantages such as high precision, easy automation, adjustable parameters, and high cleaning efficiency, can effectively remove particles such as dust, grease, and oxides on the surface of electronic components, effectively improving the durability of electronic components.
(4) Laser cleaning of cultural relics: The surfaces of cultural relics are often covered with soil contaminants, corrosion products, dust, organic stains, and crusts. These contaminants can change the chemical properties of the cultural relics and affect their appearance. Therefore, it is necessary to clean the contaminated cultural relics. Due to the preciousness and non-renewability of cultural relics, there are high requirements for the cleaning technology. Traditional cleaning methods for cultural relics mainly include chemical methods and mechanical methods, both of which will cause a certain degree of damage to the cultural relics themselves. Therefore, the laser cleaning technology for cultural relics has unique advantages such as selectivity of the cleaning object, environmental friendliness, non-contact nature, and strong controllability, and it has gradually become one of the important means for the cleaning, restoration, and protection of cultural relics.
(5) Other aspects: In the past, in the medical field, people often used chemical agents to remove patients’ tattoos. However, this method not only fails to completely remove the pigments on the skin but also harms the health of the skin. In some cases, it may even leave scars or cause inflammation. When using laser cleaning technology to remove patients’ tattoos, the laser only has a slight burning effect on the surface of the skin and will not cause serious damage to the patients’ skin. The pigment particles inside the skin will be shattered by the energy transmitted by the laser and then can be completely decomposed through the cells’ own metabolic processes, as shown in the figure.The scope of laser cleaning is constantly expanding. Currently, it has been applied to the cleaning of oil spills on the sea surface, engine carbon deposits, urban graffiti, teeth, biological warfare agents, toxic agents, and so on.
Any industry that has to provide or handle clean surfaces can benefit from the numerous advantages of laser cleaning. As a process, laser cleaning can be easily automated and integrated into the production workshop. Laser cleaning is commonly used in the following industries:
• General manufacturing industry
• Aerospace manufacturing
• Handling of nuclear contamination
• Disinfection of medical devices
• Catering industry
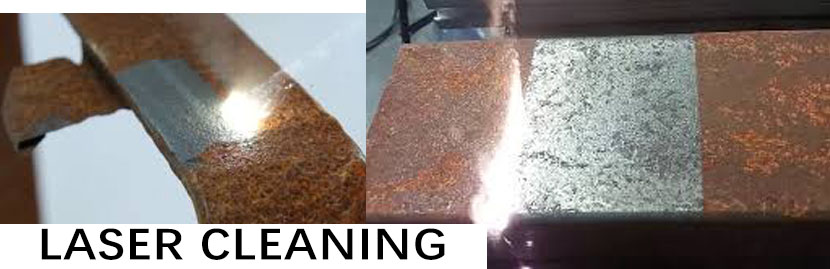
Advantages of Laser Cleaning Machine
Laser cleaning technology offers significant advantages over traditional cleaning methods. First, laser cleaning is a non-contact cleaning method, avoiding surface damage that may occur with mechanical cleaning. Second, laser cleaning does not require chemical solvents, reducing environmental pollution and health risks. Additionally, laser cleaning is highly efficient and has the potential for automation, significantly improving production efficiency and cleaning quality.
The third key term in laser cleaning is “environmentally friendly.” Pulse laser cleaning machine does not produce harmful waste during the process, aligning with modern industry’s requirements for green production. As environmental regulations become increasingly stringent, laser cleaning technology will become the mainstream choice for industrial cleaning in the future. For example, in shipbuilding, laser cleaning can replace traditional sandblasting, reducing dust and noise pollution and improving the working environment.
Other cleaning methods
● Sandblasting
Sandblasting is a common cleaning process. This method can provide an acceptable cleaning speed, but it requires expensive material handling and disposal costs. Safety is a major consideration in any sandblasting operation. Many abrasives generate a large amount of dust, requiring workers to take safety precautions including respiratory equipment and full-body personal protective equipment. The noise of the blasting process is also notoriously loud, causing serious damage to the workers’ hearing.
● Chemical cleaning
Chemical cleaning uses solvents to break down coatings and residues without damaging the underlying material. This method is usually slow and requires the material to be soaked in a chemical tank for a long time, followed by drying after the cleaning is completed. Important safety precautions such as personal protective equipment and strict disposal procedures are also required for the necessary hazardous chemicals.
● Thermal cleaning
Thermal cleaning uses relatively high temperatures to burn off the surface material. This method has high energy costs and may cause damage to the underlying material, depending on the heat resistance of the surface material and the substrate. Thermal cleaning itself cannot perform selective removal, even with the use of masks.
Future Development Trends of Laser Cleaning Machine
Since entering the 21st century, the research on laser cleaning has witnessed vigorous development. Scientists have conducted a great deal of research, ranging from the initial investigation of whether the cleaning is effective and the comparison with traditional cleaning technologies (such as mechanical cleaning and chemical cleaning), to the study of the influence of laser parameters (wavelength, energy, number of pulses, incident angle, etc.) on the cleaning effect, the evaluation of the cleaning effect using various detection methods (ellipsometer, Auger electron spectroscopy, spectroscopy, etc.), and the analysis of the causes of the cleaning mechanism, and have obtained useful conclusions.
As can be seen from the above introduction, the effect of laser cleaning has been recognized. There is relatively more research in the fields of microelectronics and cultural relic protection. Meanwhile, various cleaning objects have been attempted, including substrate materials such as metals, optical glass, and composite materials, and contaminants such as particles, paint, and oxide layers. In addition to excimer lasers, CO₂ lasers, and Nd:YAG lasers, the use of fiber lasers has also increased.
Before, during, and after laser cleaning, the cleaning effect and process can be judged through various monitoring means. The monitoring of laser cleaning of cultural relics was carried out earliest, and then other types of cleaning gradually introduced monitoring as well. Commonly used monitoring technologies for detecting the cleaning effect and efficiency of laser cleaning include imaging technology and spectroscopic technology, etc. Imaging technology can be achieved through direct observation, photography, optical microscopy, electron microscopy, etc. Spectroscopic technology can obtain the composition of the cleaning object before and after cleaning as well as the compositional changes during the cleaning process by analyzing absorption spectra, reflection spectra, Fourier transform infrared spectra, laser-induced plasma spectra, etc. It is also possible to know the cleaning effect by measuring the surface information of the object, such as electron paramagnetic resonance technology, hardness tester, particle size analyzer, etc.
Monitoring includes both detection and control. The purpose of detection is to determine the cleaning process and judge the cleaning effect, while control is to adjust the cleaning parameters and process according to the detection results to ensure a good cleaning effect. Detection can be divided into offline monitoring and online monitoring. The former is to detect the sample after the cleaning is completed, and the latter, combined with the control system, conducts monitoring during the cleaning process and judges the cleaning effect by detecting relevant parameters. Online detection requires data processing, analysis, and judgment based on the online measurement results, and then controls the laser cleaning process. Compared with offline monitoring, online monitoring has higher requirements and greater difficulties. In the future, intelligent control based on the online detection system will become the mainstream research direction.
With the continuous advancement of laser technology, laser cleaning technology is also evolving and improving. In the future, laser cleaning will develop towards higher power, shorter pulses, and greater intelligence. High-power lasers will enhance cleaning efficiency, making them suitable for cleaning larger areas and thicker contamination layers. Ultrashort pulse lasers will achieve finer cleaning effects, meeting the requirements of high-precision fields. Intelligent laser cleaning systems will integrate artificial intelligence and machine vision technologies, enabling automatic recognition and cleaning, further improving cleaning precision and efficiency.
Moreover, the application areas of laser cleaning technology will continue to expand. For example, in the medical field, laser cleaning can be used for the disinfection and cleaning of medical instruments, ensuring medical safety. In the energy sector, laser cleaning can be applied to clean solar panels, improving energy conversion efficiency. In the construction industry, laser cleaning can be used to clean building exteriors, extending the lifespan of structures.
Conclusion
With the increasing demand for green, environmentally friendly, high-precision, and high-efficiency cleaning, the research, development, and application of laser cleaning technology have received more and more extensive attention. At present, laser cleaning technology has been applied in fields such as microelectronics, rail transit, aviation, and cultural relic restoration. However, to further expand its application scenarios, scale, and effectiveness, many challenges still lie ahead, including:
(1) The mechanism of laser cleaning needs to be further improved. There is an urgent need to establish a complete theoretical model of laser cleaning to enhance the simulation effect of laser cleaning.
(2) The intelligent system for real-time monitoring and evaluation needs to be strengthened. Currently, the functions of laser cleaning equipment are relatively simple, and the degree of intelligence is insufficient. It is possible to further integrate the laser system with automated systems such as identification and positioning, online monitoring, and robots to improve the cleaning efficiency.
(3) The research, development, and application related to hybrid cleaning urgently need to be enhanced. Due to the complex surface conditions of the objects to be cleaned and the numerous factors affecting the effect of laser cleaning, implementing a highly versatile hybrid cleaning process for engineering applications is conducive to achieving composite cleaning and balancing efficiency, effectiveness, and cost.
In conclusion, laser cleaning technology has broad development prospects and will be applied in more fields in the future. With the progress of technology and the expansion of market share, its scale and industrialization level will be further improved.
As an efficient, environmentally friendly, and precise cleaning method, laser cleaning technology is playing an increasingly important role in modern industry. Its advantages of high energy density, precision cleaning, and environmental friendliness make it an ideal replacement for traditional cleaning methods. With continuous technological advancements and the expansion of application areas, laser cleaning will play an even more significant role in future industry, driving industrial cleaning towards a greener, smarter, and more efficient direction.
Through this article, we hope you have gained a deeper understanding of laser cleaning technology. Whether in aerospace, automotive manufacturing, or cultural heritage preservation, laser cleaning has demonstrated its unique advantages and application potential. Let us look forward to the widespread application of laser cleaning technology in future industry, contributing to green production and sustainable development.
由用户投稿整理稿件发布,不代表本站观点及观点,进行交流学习之用,如涉及版权等问题,请随时联系我们(yangmei@bjjcz.com),我们将在第一时间给予处理。